A crucial aspect in designing Controlled Environment Agriculture (CEA) systems is in understanding the lighting component. Accurately modeling the lighting requirements allows growers the ability to calculate cost of ownership, return on investment, and better understand how light and light equipment tie into profit and loss of the final product – salable biomass.
In this report, the complexities of modeling CEA systems is broken down into two component parts which are the major energy conversions in horticulture lighting. These conversions are electricity to photon (light fixture) and photon to biomass (salable crop production). In future papers, these individual systems will be examined in closer detail, allowing the grower the capability to compare lighting options from either a birds-eye-view, or down to the details of complex system interactions.
Table of Contents
- Introduction
- Electricity (Watt) to Light Energy (Photon) Conversion
- Light Energy (Photon) to Plant (Biomass) Conversion
- Summary
- References
1. Introduction
Lighting for horticulture applications has increased in both sophistication and efficiency over the years. This has been due to a better understanding of the interaction of photons and plants as well as innovations in lighting technology and design. Still, there is much confusion and debate in regards to the best lighting option for each situation. This paper takes a look at the major components and factors involved regarding the relationship between lighting and plants. The goal is to have a dynamic model that can account for different applications, different environments, and different available inputs which will allow the system designer and grower to predict future outcomes and cost based on unit operations and parameter inputs. Figure 1 shows the two major energy conversions in horticulture lighting, the conversion of electricity to photons and the conversion of photons to biomass.
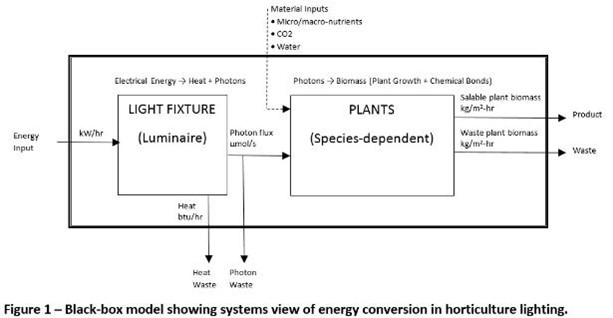
2. Electricity (Watt) to Light Energy (Photon) Conversion
The first energy conversion shown in Figure 1 occurs within the light fixture where the energy is converted from electricity to photons and heat. The term luminaire is carried over from the non-horticulture lighting industry, and refers to light fixture.
Energy input
Each fixture draws in a certain amount of energy as watts. In modeling the grow system this should be the actual measured input, not what the lighting manufacturer lists, as there can be significant variance due to environmental conditions. The output is photons over time in PPF (µmol/s), and should be measured over the range of photosynthetically active radiation (PAR), which is typically 400-700 nm. The conversion from watts to photon energy is not 100% efficient, and depending on the fixture type and components, much of the energy is converted to wasted heat. One simple ratio used to compare fixtures is the PPF out divided by the watts in. Since watts are equivalent to joules/second (J/s), this ratio becomes (µmol/s) / (J/s) = µmol/J.
Heat Waste
All light fixtures give off waste heat, some more than others. It should be noted that several indoor growing facilities rely on this heat for heating the environment. This is not encouraged, as there are many more efficient means to heat and cool a room. Fixtures that produce significant heat require more HVAC cooling and heating to counteract the lights turning on and off throughout the day.
Photon Waste
The photon waste stream in Figure 1 includes photons that are lost either because (1) they are the wrong wavelength, (2) they are not directed to the plant canopy, or (3) they are lost or diluted over area because of the distance between the light fixture and the plant canopy.
- (1) Different types of lamps (bulbs) and LEDs emit different wavelength spectrums of light. The number, quality, and period of photon emissions which are useful to the plants depend greatly on the types of plants themselves and what stage of development they are in.
- (2) Photons are wasted if they hit places that are not part of the plant canopy. This occurs where light hits the walls, walkways, and spaces in-between the plant canopy. High Intensity Discharge (HID) fixtures use reflectors to best reflect light emitted from the top of the bulb down to the plant canopy. LED manufacturers often use LED optics, which are small micro-sized structures placed over the chips, which direct the light generated from the LED towards the canopy. The types and number of reflectors and optical layers contribute towards reduction in the amount of photons that are emitted. Growers sometimes use reflective surfaces to allow photons to reflect off of walls back towards the canopy. If possible it is more efficient to direct the light towards the canopy at the fixture level because this is where the light density is the greatest and with each reflection there is significant loss in photon energy.
- (3) The air medium by which the light travels results in a diminishment of photons. The further the light fixture from the plant canopy, the more photons are lost from frequent scattering, which is known as attenuation (a much stronger factor in water than air). This is different than the spreading of light over an area as distance increases. The decrease in PPF over an area due to the light spreading as the distance increases is known as the inverse square law. For these reasons, the distance the lights are placed away from the canopy greatly determines how many photons, and the density of these photons, make it to the plants.
3. Light Energy (Photon) to Plant (Biomass) Conversion
The second energy conversion occurs in the plants. Figure 2 shows the inputs and outputs in an actual vertical growing system. The energy conversion from photons to plant biomass is through the process of photosynthesis. Photoreceptors in the plants also react to photons of different wavelengths and these elicit physiological changes and responses that help to direct the development of the plant.
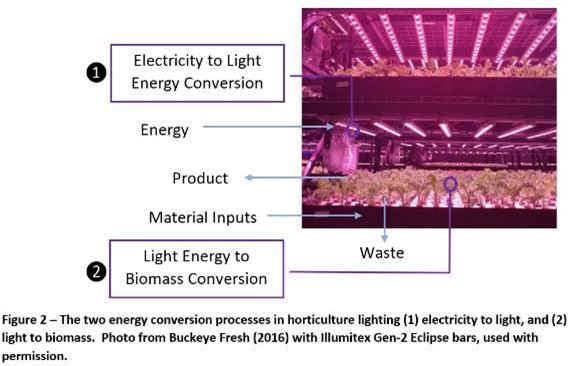
The conversion from photon to chemical bond energy can be calculated by taking the ratio of chemical bond energy in the salable portion of the harvested plant to the photon energy received at the plant canopy. In a study by Kozai et al. (2013), this is referred to as the Light Use Efficiency (LUE) and was found to be 0.027 in a vertical growing system. In this example, 2.7% of PAR energy is converted to chemical energy in the plant. The rest of the PAR energy either was not the most efficient wavelength for photosynthesis, was not able to be taken up by the plant, was lost by hitting a portion of the canopy without leaves, or the energy was metabolically consumed by the plant for all the reactions needed to stay alive. The salable portion of the plant will differ significantly depending on the type of plant product being sold. Also, since some molecules are more energetically expensive to synthesize, the LUE could differ just based on the nutritional or nutraceutical content of the salable biomass.
The portion of the biomass that is not salable is wasted biomass. Usually, the wasted biomass is also weighed, allowing the grower to know the fraction of salable to wasted biomass due to a certain set of parameters. In a controlled environment agricultural system, the wasted biomass can be utilized for energy and/or recycling of nutrients.
Material inputs
The two energy conversion steps of the model are also involved in complex interactions with other environmental conditions such as humidity, micro/macro-nutrient availability, pH, CO2, water, air flow, etc. The major material inputs for photosynthesis and the conversion of photons to chemical bonds are water, CO2, and micro/macro-nutrients. As light energy increases, more water and CO2 are needed to keep up with photosynthesis. Without enough of these inputs, the photons can become damaging to the plant cells. The amount of micro/macro-nutrients is also crucial for photosynthesis and proper cell function under different light conditions.
Besides material inputs and their interactions with light, the environmental conditions play a large role in the way in which plants utilize light. Additional heat coming off of HID lamps causes the canopy to rise in temperature, which then lowers humidity, alters transpiration and CO2 levels, and photosynthetic rates. When growers switch from HID to LED, this influences multiple responses in the plant, which can be deleterious to productivity if not managed correctly. This complex interaction of parameters is why it helps to have trusted horticulture lighting manufacturers with growing experience and resources to assist the grower in this complicated transition.
Time component
Finally, it is important not to model the energy conversions as a static point in time. The light output of some some light fixtures and bulbs decreases over time and can shift in color. Also, plants require different light amounts and quality over their growth cycle. Other components, such as dust, can accumulate causing light output to decrease. For these reasons horticulture lighting systems that compare inputs and outputs for different fixtures and crops should carefully state time periods that are representative of what the grower can expect to encounter.
4. Summary
Understanding the interaction of inputs to outputs in the 2-step conversion of electricity to photons and photons to biomass can be challenging. The light fixtures can be compared to each other but the way in which the output of different light fixtures (heat and photons) affect plants over time can be quite complex. This paper outlines those complexities and serves as a starting point for digging deeper into individual portions of the systems model. Ultimately, the decision for which light fixtures to use has to do with application. With accurate models, growers can consider all the inputs and outputs, the interactions, and the timing for all parameters when making the decision for which horticulture light is right for them. The next paper will consider an analysis of the spectrums and calculation of useful photons emitted by different light fixtures.
5. References
- Hopkins, William G. and Norman P. A. Hüner. (2009) Introduction to Plant Physiology. 4nd ed. New York, NY: John Wiley & Sons.
- Knight, Rebecca. “Modeling the Unknown – Why Light Calculations are So Hard” https://www.illumitex.com/modeling-unknown-light-calculations-hard-779.
- Kozai, T. (2013). “Resource use efficiency of closed plant production system with artificial light: Concept, estimation and application to plant factory.” Proceedings of the Japan Academy, Series B 89(10): 447-461.